Wet Basement with Fieldstone Foundation, Haverhill, MA
Challenge
Many homes in the North Shore Massachusetts area were built in the late 1800s. While this gives New England homes a lot of charm, it also leaves many of today's homeowners needing to make upgrades and repairs as they purchase the properties. The home in question for this case study is located in Haverhill, Essex County, Massachusetts. It was built in the 1890s, and the current homeowner Jeff has lived there with his family since 2008.
Over the years, Jeff had reached out to a handful of general contractors to address the growing list of issues the home was facing with its basement. However, none were qualified to take on the work or provide lasting, permanent solutions. Some of the main concerns were;
- a leaning, fieldstone foundation wall
- sagging floors and floor joists
- wet basement - existing waterproofing system was a simple pump in an open hole in the floor
- moisture and wet air in the basement
The first challenge on the list was the failing, fieldstone foundation wall. Over the years, soils on the exterior of the wall shifted with each season - freezing in the winters, expanding as they absorbed water in the spring, and drying out in the warmer months. As this cycle continued, eventually the soils expanded and applied pressure to the fieldstone wall, forcing it to buckle inwards.
Next up, are the sagging floors. The homeowners mentioned their floors were increasingly growing louder with creaks and cracking sounds and became more and more uneven and wavy in various sections throughout the home. The supports beneath the floors were replaced over the years, and at the time of Erickson's inspection comprised of mostly lally columns, but also a number of temporary jack posts. While lally columns themselves are strong and capable, the layout of these columns in the basement was incorrect and did not provide the necessary support. However, the jack posts were noticeably failing to correctly support the weight of the floors above them.
The third challenge mentioned was having a wet basement. The existing sump pump was removing water from the basement, however, the system was not capturing all the water entering the space. Water was entering the basement from both the walls and through the floor, as the water table on the ground was noticeably high. The sump pump was kept in a bucket on the floor, so not only was the system not capturing all the water, but it also looked terrible and unsafe.
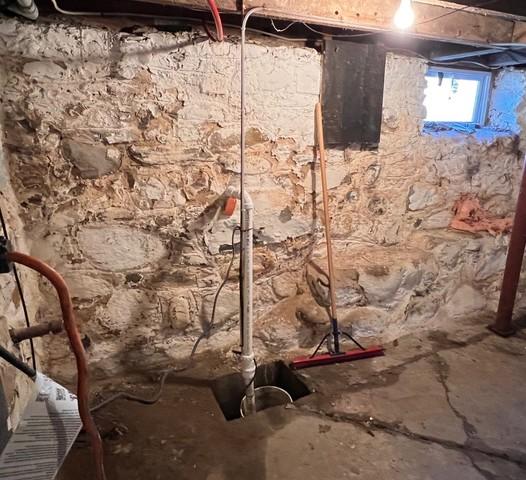
Since the waterproofing system was incomplete and allowed for water to sit open in the basement, the final challenge involved improving the air quality in the basement. The air was full of moisture, which would inevitably lead to rot and mold, as well as poor air which would enter the home living space above.
Overall, it was an old home with an old basement that needed some upgrades in order to improve the quality of life for the homeowners.
Solution
Erickson Foundation Solutions' design and inspection specialist for this project was Michael Bradley. Noting all of the challenges mentioned, Mike designed and proposed the following systems and solutions to address the homeowner's concerns;
- The bowing, fieldstone foundation wall was more than 100 years old and about 1' in thickness. It had a small window, and also had the home's HVAC unit connecting through it. The HVAC unit had to be temporarily disconnected and removed. The sump pump also had to be temporarily removed. With fieldstone foundation walls, the overall integrity of the material is unpredictable. In most cases, it is not advisable to try and remove sections or cut into the wall, as it may cause a chain reaction of crumbling or collapse. Over the years, Erickson developed a solution for fieldstone foundation walls, by installing a secondary auxiliary concrete wall. Mike designed this wall to be 3' wide (due to an 18" high knee wall on the bottom portion of the wall), and reinforced it with steel PowerBraces, spaced about 6' apart, as well as with rebar. This new auxiliary wall spanned the entire length of the wall (21' 6") and was secured to both the floor and the floor joist system above with steel brackets and large lag bolts.
Auxiliary Wall Construction Auxiliary Concrete Foundation Wall - To address the sagging floors, Mike's design included 15 SmartJacks and 40ft of supplemental beam support. 5 of the SmartJack's were replacing load-bearing lally columns, and the other 10 were additional supports to help lift the sagging floors and make them level again.
SmartJack's and Supplemental Beam - While the basement had an existing sump pump, it was not correctly doing the job. Water was entering the basement through the walls and the floor, but not all of this water was making its way to the sump pump basin. The basin itself was just a bucket on the floor, the sump pump sitting exposed at the bottom. To upgrade this system and correctly capture the water entering the basement, more than 50' of perimeter WaterGuard was installed along the base of the entire basement. The pump itself was upgraded to a TripleSafe sump pump with a battery backup.
TripleSafe Sump Pump and Battery Backup - One of the final challenges to address in the basement was the moisture in the air. Adding the upgraded sump pump and WaterGuard system was a big help, but did not completely solve the problem. The foundation walls in various locations throughout the basement showed signs of water entering. To contain this water and moisture, as well as direct it to flow into the perimeter WaterGuard drains, CleanSpace Wall Vapor Barrier was installed. This durable vapor barrier system effectively wraps the walls and contains the moisture which otherwise would enter the basement and allow for rot and mold to take hold. Approximately 2,300 sq. ft. of CleanSpace was installed.
CleanSpace Wall Vapor Barrier
Project Summary
Design Specialist/Inspector: Michael Bradley
Crew Leads: Ed Nadreau, Nick Carelli
Products Installed: SmartJacks, Supplemental Beams, TripleSafe Sump Pump w/ Backup Battery, WaterGuard, Auxiliary Wall, PowerBraces, SaniDry Dehumidifier, CleanSpace Wall Vapor Barrier
Contractor: Erickson Foundation Solutions